
Construction Asset Tracking Software: The Ultimate 2025 Guide
by nuVector • 3/14/2025 • Last Updated: 3/25/2025
Imagine a $50,000 excavator vanishing overnight or essential tools gradually disappearing, draining your budget as deadlines loom. These losses don’t just disrupt schedules—they erode your bottom line. In 2025, construction asset tracking software isn’t just a convenience; it’s a necessity for firms that want to stay competitive, efficient, and profitable.
This technology provides real-time visibility into your equipment, tools, and materials, helping you prevent theft, reduce downtime, and optimize resource allocation. The result? Lower costs, increased productivity, and seamless job site management.
Whether you’re a small contractor or managing multi-site operations, this ultimate guide will break down everything you need to know: how construction asset tracking works, why it’s transforming the industry, and how you can implement it for maximum impact. Packed with actionable insights, real-world examples, and future trends, this guide will prepare you to dominate in 2025.
Let’s dive in!
What Is Construction Asset Tracking Software?
At its core, construction asset tracking software is a digital solution that keeps tabs on your equipment, tools, and materials across construction sites, warehouses, and supply chains. It leverages advanced technologies like GPS, RFID, barcode scanning, and IoT sensors to deliver real-time data on where your assets are, how they’re being used, and their overall condition—think of it as a GPS for your bulldozer or a health monitor for your power tools.
Unlike traditional methods—such as handwritten logs or frantic visual checks—that are prone to errors and delays, this software automates the entire process, minimizing mistakes and saving you time. For construction firms in 2025, it’s the difference between guessing and knowing, ensuring you have full control over your assets no matter where they are.
Core Features That Deliver Results
- Real-Time Location Tracking: Find assets instantly—whether it’s a crane on-site or a generator in transit.
- Condition Monitoring: IoT sensors flag issues like wear, temperature changes, or damage before they cause trouble.
- Automated Inventory: Syncs asset data to eliminate manual counts and prevent over-ordering.
- Scalability: Grows with your business, from a handful of tools to a fleet of heavy machinery.
The Top Benefits for Construction Businesses
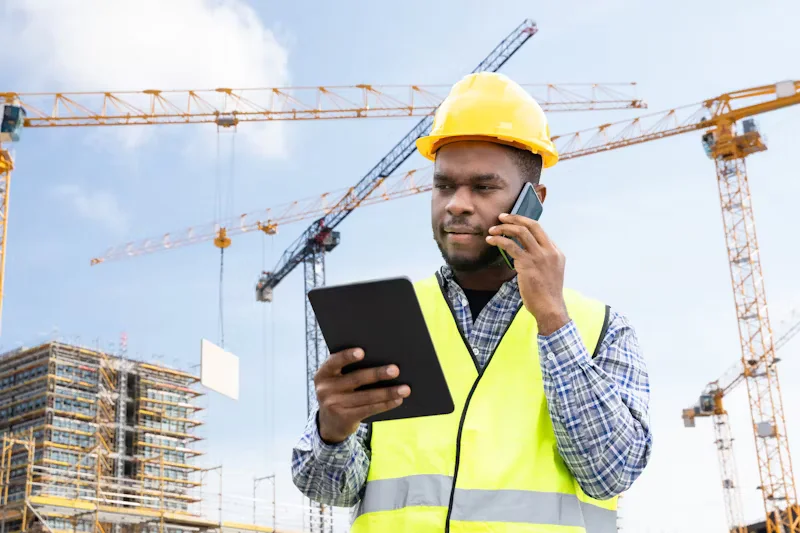
Managing a construction project means balancing tight schedules, high equipment costs, and the constant risk of theft. Without the right systems in place, valuable resources can slip through the cracks—leading to costly delays and budget overruns. Asset tracking software brings order to the chaos, offering real-time visibility and control over your equipment, tools, and materials. Here’s how it transforms your operations:
1. Reduce Costs and Prevent Equipment Loss
Missing or stolen equipment can drain your budget fast. The National Equipment Register (NER) estimates that construction site theft costs the industry up to $1 billion annually, with an average loss of $30,000 per stolen item. Asset tracking software drastically reduces these risks by sending real-time alerts when unauthorized movements are detected, helping you recover lost assets and avoid unnecessary replacements.
2. Strengthen Security with Geofencing Alerts
Construction sites are prime targets for theft, especially when expensive equipment is left unattended overnight or in remote locations. Geofencing technology sets virtual boundaries around your job site—if a tracked asset moves beyond its designated area, you receive an instant alert. Companies using asset tracking software experience significantly lower theft rates, protecting their investments and keeping projects on schedule.
3. Boost Productivity and Job Site Efficiency
Every minute spent searching for misplaced tools or manually logging inventory is time wasted. Asset tracking software streamlines operations by automating inventory checks, pinpointing asset locations in seconds, and predicting maintenance needs. Research from Research Gate shows that companies using real-time equipment monitoring improve asset utilization by up to 30%—ensuring that tools and machinery are always where they’re needed most.
4. Scale Seamlessly as Your Business Grows
Whether you’re a small contractor managing a handful of tools or an enterprise overseeing a fleet of heavy machinery, construction asset tracking software grows with you. Start by tracking your most critical assets—like generators or excavators—and expand as your operations scale. With cloud-based solutions, you can monitor assets across multiple job sites in real time, ensuring nothing gets lost in the shuffle.
5. Improve Sustainability and Regulatory Compliance
Asset tracking doesn’t just help with security—it also plays a crucial role in sustainability and compliance. By optimizing equipment usage and reducing unnecessary wear and tear, you extend asset lifespans and minimize waste. Many solutions also generate automated reports, making it easy to maintain compliance with industry regulations, log asset movement, and pass audits without the headache of manual record-keeping.
How It Works: Technologies, Processes, and Best Practices
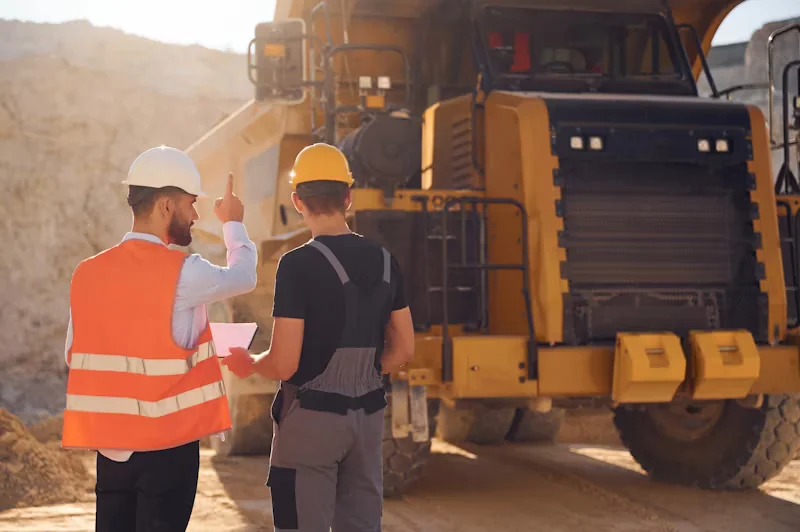
Curious about how construction asset tracking software keeps your equipment, tools, and materials in check? Let’s break down the cutting-edge technologies, step-by-step processes, and best practices that make it an essential tool for modern construction businesses.
Technologies Powering Construction Asset Tracking
- GPS Tracking: Uses satellite technology to provide precise location data for mobile assets like trucks or cranes, ideal for tracking across multiple job sites or during transit.
- RFID Technology: Enables bulk scanning of assets with RFID tags—perfect for quickly logging hundreds of tools or materials in seconds, reducing manual effort.
- Barcode Scanning: A cost-effective method for smaller operations, using handheld devices to scan barcodes on tools or materials for quick inventory updates.
- IoT Sensors: Monitors asset conditions like vibration, temperature, or wear, predicting maintenance needs to prevent costly breakdowns.
- Cloud Platforms: Centralizes data for access from anywhere, ensuring real-time updates and seamless team collaboration.
The Asset Tracking Process
Implementing asset tracking software isn’t just about installing devices—it’s about creating a system that keeps your job sites efficient and organized. By following these steps, you can ensure that every piece of equipment is accounted for, properly maintained, and optimized for maximum productivity.
- Tag and Track Assets Instantly: Attach GPS trackers to heavy machinery, RFID tags to pallets, and barcodes to tools, ensuring every asset is logged and easily traceable.
- Take Proactive Action Before Problems Arise: Get instant alerts when assets move unexpectedly, require servicing, or are due for inspection—preventing downtime and costly delays.
- Analyze Usage and Identify Inefficiencies: Detailed reports provide insights into underutilized equipment, maintenance needs, and workflow bottlenecks to cut costs and improve resource allocation.
Manual vs. Software-Based Tracking
The difference between outdated manual tracking and modern asset tracking software is night and day. Below, we break down how software-driven solutions outperform traditional methods in every critical area—helping you cut expenses, boost efficiency, and protect your assets.
Aspect | Manual Tracking | Software-Based Tracking |
---|---|---|
Cost | Drains budgets with labor-heavy processes and frequent errors | Cuts expenses by automating tracking and reducing costly mistakes |
Efficiency | Slows projects with time-consuming searches and unreliable records | Speeds up operations by instantly locating assets and updating records |
Security | Leaves assets vulnerable to theft and unauthorized use | Enhances security with real-time monitoring and geofencing alerts |
Scalability | Becomes unmanageable as projects and teams grow | Scales effortlessly, from small teams to enterprise-level operations |
Data Accuracy | Prone to human error, leading to poor planning and costly miscalculations | Provides precise, real-time data for better decision-making |
Maintenance | Reactive approach leads to unexpected breakdowns and costly delays | Prevents downtime with predictive maintenance and automated scheduling |
Best Practices for Success
Construction asset tracking software is a game-changer—but only if used effectively. The right strategies ensure you’re not just tracking assets, but actively reducing losses, improving efficiency, and protecting your bottom line. Follow these best practices to get the most out of your system.
-
Track What Matters Most: Start with high-value or frequently misplaced assets—excavators, generators, and power tools. Tracking your most expensive or theft-prone equipment first delivers immediate savings by reducing downtime and losses. For example, securing a bulldozer often targeted for theft or a generator frequently left behind ensures your biggest investments stay productive and protected.
-
Keep Your Data Clean: Your system is only as good as its data. Perform regular audits—scrubbing duplicates, correcting errors, and updating asset statuses—to ensure records reflect reality. Inaccurate tracking can lead to misplaced equipment, unnecessary orders, and wasted resources. A well-maintained database helps you make smarter decisions, from scheduling repairs to reallocating machinery across job sites.
-
Set Smart Alerts: Prevent issues before they happen with real-time notifications. Use geofencing to create virtual site boundaries and get instant alerts if a tracked asset—like a crane or tool trailer—moves off-site unexpectedly. Pair this with maintenance reminders that flag when equipment needs servicing, preventing costly breakdowns and project delays. Smart alerts turn your tracking system into a proactive problem-solver.
-
Train Your Crew for Success: The best system is useless if your team doesn’t know how to use it. Hold quick, hands-on training sessions to teach workers how to log assets, respond to alerts, and track equipment status. A foreman who can instantly locate a missing welder or flag an overdue maintenance check is more efficient and confident. Regular training keeps your team engaged, ensuring your system is fully utilized across every project.
By focusing on high-value assets, maintaining accurate data, leveraging proactive alerts, and ensuring your team is well-trained, your asset tracking software becomes more than a tool—it becomes a competitive advantage. Implement these strategies, and you’ll see stronger security, reduced costs, and smoother operations as you scale into 2025 and beyond.
Step-by-Step Guide to Implementing Asset Tracking
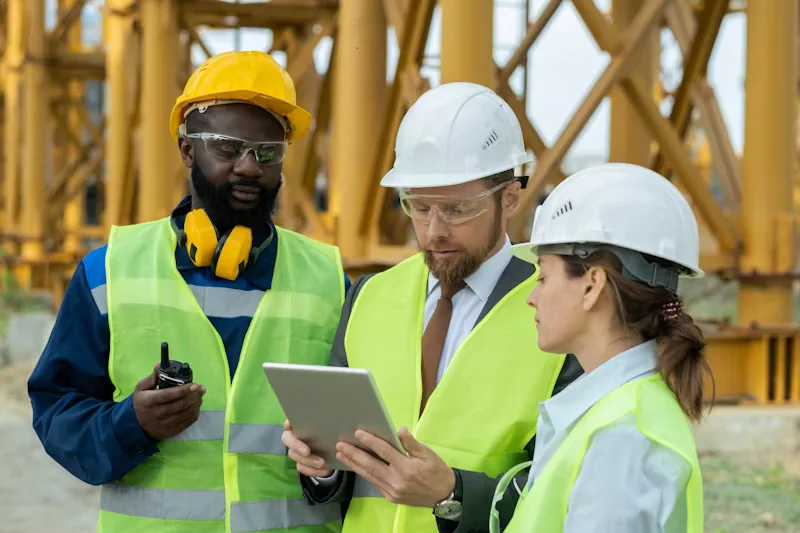
Implementing construction asset tracking software doesn’t have to be overwhelming. Follow this structured roadmap to ensure a seamless rollout and maximize its impact.
Step 1: Identify Your Challenges and Set Clear Goals
- Pinpoint your biggest asset management problems—frequent theft, equipment downtime, or inefficient inventory tracking.
- Set measurable goals, such as reducing losses by 20% or cutting downtime by 15%, to guide your implementation strategy.
Step 2: Choose the Right Tracking Technology
- Select technologies that fit your needs:
- GPS: Ideal for tracking mobile assets like trucks and cranes across multiple job sites.
- RFID: Best for bulk tracking tools and materials efficiently on-site.
- Barcodes: A cost-effective solution for keeping tabs on smaller tools and inventory.
- IoT Sensors: Enables real-time condition monitoring for heavy machinery, preventing unexpected breakdowns.
- Ensure your software is scalable so it can grow with your business.
Step 3: Tag and Deploy Your Assets
- Attach trackers based on asset type—GPS for heavy equipment, RFID for pallets, and barcodes for hand tools.
- Start with a pilot project on one job site to test functionality, refine processes, and address any issues before full deployment.
Step 4: Integrate with Existing Systems
- Use nuVector’s asset tracking software for real-time data, geofencing, and centralized reporting—eliminating the need for multiple platforms.
- Ensure seamless integration with construction management tools to create a single, unified system from field to office.
Step 5: Train Your Team for Success
- Conduct quick, hands-on training (15–30 minutes) covering how to:
- Log assets
- Respond to alerts
- Navigate dashboards
- Provide a simple reference guide for ongoing support and ensure continuous adoption.
Step 6: Monitor, Analyze, and Optimize
- Regularly review weekly reports to spot underutilized assets, maintenance needs, and potential inefficiencies.
- Use these insights to reassign idle equipment, schedule proactive maintenance, and refine workflows for better efficiency.
Step 7: Scale as Your Business Expands
- Gradually expand tracking to new sites and additional assets as your operations grow.
- Implement advanced features like AI-driven analytics to further enhance efficiency and cost savings.
Pro Tip: Maximize security by placing trackers on high-risk assets near site exits or high-traffic areas—helping prevent theft before it happens.
Future Trends in Construction Asset Tracking for 2025 and Beyond
Construction asset tracking is evolving faster than ever, driven by cutting-edge technology that enhances efficiency, security, and automation. Here’s what’s shaping the future of the industry:
-
AI-Powered Optimization: Artificial intelligence will predict equipment needs, automatically adjusting resource allocation to minimize idle time and maximize efficiency. Expect smarter scheduling, ensuring every asset is deployed at the right time—without the guesswork.
-
Next-Gen IoT Sensors: Enhanced real-time monitoring will track wear, temperature, and vibrations with unprecedented accuracy. This means fewer breakdowns, longer equipment lifespans, and seamless preventive maintenance to keep projects moving.
-
5G-Enabled Connectivity: Supercharged real-time tracking across multiple job sites will become the norm. With lightning-fast data transfer, construction firms will experience flawless coordination, instant alerts, and improved site-wide visibility, no matter the scale.
-
Blockchain for Unbreakable Security: Blockchain technology will lock in tamper-proof asset records, ensuring 100% data integrity while simplifying compliance and audits. This secure, transparent system will build trust across teams and stakeholders, reducing disputes and streamlining asset management.
Protect Your Construction Assets and Boost ROI With LoopManager
In 2025, construction asset tracking software isn’t just a tool—it’s a necessity. The ability to monitor equipment in real time, prevent losses, and schedule predictive maintenance means lower costs, higher efficiency, and fewer project delays.
With nuVector’s returnable asset tracking software, you get an industry-proven, all-in-one solution trusted by major brands like Chep, Sonoco, Warner Bros among others. Whether you’re managing tools, heavy machinery, or materials, LoopManager helps you eliminate inefficiencies and take control of your assets with precision.
Don’t let misplaced equipment or unexpected downtime slow you down—upgrade your asset management today!
>> Book Your Free Demo with nuVector Today!
FAQ: Everything You Need to Know About Construction Asset Tracking
What defines construction asset tracking software?
Construction asset tracking software monitors equipment, tools, and materials using GPS, RFID, and barcode scanning in real time. This technology empowers firms to manage assets across job sites, minimizing losses and boosting productivity through automated inventory—perfect for keeping cranes, tools, or materials under control with precision.
How does construction asset tracking software enhance project efficiency?
Construction asset tracking software delivers live location data, automates inventory management, and anticipates maintenance needs—reducing downtime significantly.
How does construction asset tracking software prevent theft on job sites?
Construction asset tracking software employs geofencing to establish virtual boundaries, sending instant alerts if assets move outside designated zones—stopping theft before escalation. A firm could swiftly recover stolen equipment, safeguarding investments with proactive, vigilant technology.
How does construction asset tracking software support sustainability?
Construction asset tracking software prolongs asset life and streamlines logistics, reducing waste and emissions for greener operations. A firm might noticeably decrease material waste, saving resources and aligning with eco-friendly goals while maintaining top performance.
What should construction firms seek in asset tracking software?
Construction firms should prioritize scalability, real-time tracking capabilities, and features like geofencing or IoT sensors when choosing asset tracking software. Selecting a solution that fits budget needs and includes training support ensures teams maximize efficiency from day one.