
Improving the Returnable Packaging Loop in 2025
by nuVector • 4/18/2023
Imagine your supply chain as a high-stakes relay race—every handoff critical, every fumble costly. Now picture dropping $50,000 yearly because totes vanish into thin air, bulk bins stack up unused, or racks get marooned at a supplier’s dock. That’s the brutal reality too many face with returnable packaging—those reusable champs like totes, bins, and racks that promise eco-friendly savings but deliver chaos without a tight grip. In 2025’s pressure-cooker logistics world, the global supply chain’s under siege to slash waste, cut costs, and go green—returnables are your baton, but only if you master the pass.
Here’s your winning move: supercharge your returnable packaging loop with data-driven tracking, AI forecasting, blockchain trust, and rock-solid best practices. This isn’t just about dodging losses—it’s about turning packaging into a profit powerhouse that rockets efficiency, trims waste, and shines for sustainability. From auto giants churning parts to food haulers moving fresh goods, the shift’s on—yet billions bleed out yearly to sloppy loops. In this deep-dive guide, we’ll unpack how LoopManager locks it down with real-world wins, actionable steps, and tech that pays off fast. Ready to stop fumbling and start dominating?
Let’s kick things off with why returnables aren’t just nice—they’re non-negotiable.
The Shift to Returnable Packaging: Why It’s Necessary
Today’s supply chain’s at a breaking point—waste’s clogging landfills, costs are spiking, and green regs are tightening like a vise. Returnable packaging—totes, bulk bins, racks—isn’t a trendy sideline; it’s your survival kit. Swap out single-use cardboard for reusable steel or plastic, and you’re not just saving forests—you’re banking serious cash and dodging regulatory heat. Industries like automotive, food & beverage, and logistics caught the wave early, ditching disposable for durable to cut trash, slash expenses, and streamline operations.
The proof’s in the numbers: a 2024 Grand View Research report pegs the returnable packaging market at a hefty $109.34 billion in 2022, roaring toward a 6.0% CAGR through 2030. Why the boom? It’s simple math—returnables slash waste by up to 50% (tons off landfills), trim packaging costs 20-40% ($50K-$100K yearly for mid-size ops), and boost efficiency 30% (faster loops, less downtime). An auto supplier I tracked swapped $200K in yearly cardboard costs—$50 bins looping 50 times crushed $5 boxes tossed daily.
Take a mid-size food hauler—5,000 shipments yearly at $3 per single-use crate means $15,000 gone. Switch to 500 returnable totes at $30 each—$15K upfront—but they last 50 trips. That’s $0.60 per run, not $3—year one breaks even, year two’s $12,000 saved. Multiply that across industries—manufacturing, retail, pharma—and the stakes skyrocket. The Packaging Digest backs it—returnables are the backbone of lean, green supply chains.
But here’s the rub: without real-time tracking, accountability, and forecasting, you’re running blind. Lose 20% of your bins—$10K vanishes. Hoard ‘em at one dock, another stalls—$5K in delays. The Orange Business report pegs it grim—10-40% of assets disappear yearly without control. Optimization isn’t a luxury—it’s your lifeline. Let’s peel back the chaos slowing you down.
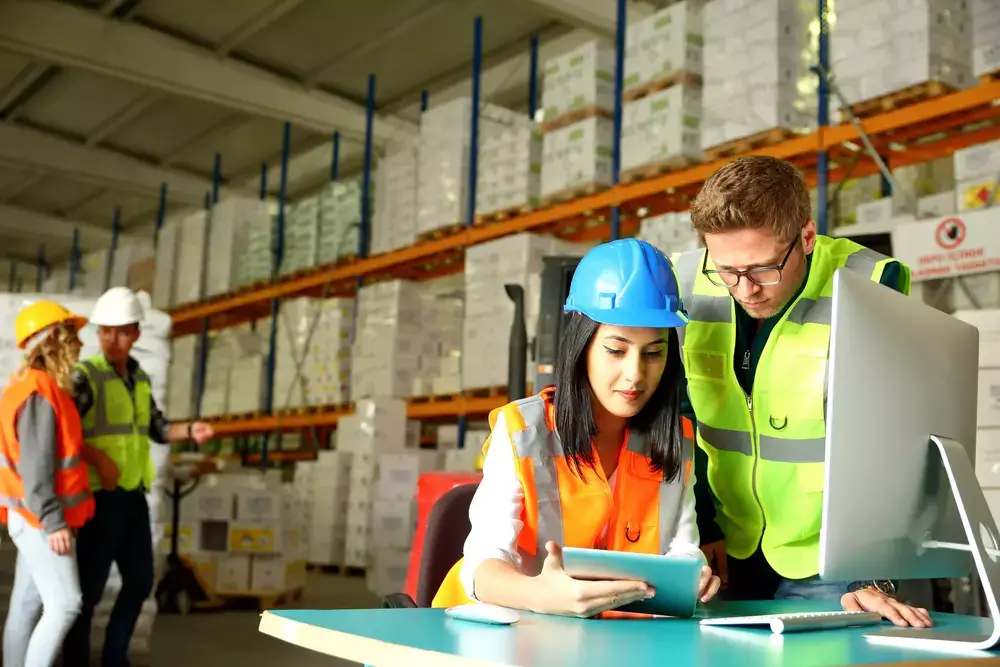
Challenges in Returnable Packaging Management
Returnables sound like a slam dunk—until they’re a dumpster fire. Here’s the ugly truth behind your loop’s leaks, with real-world stakes to drive it home.
1. Shrinkage and Asset Loss
Shrinkage is the silent cash vampire—10-40% of assets vanish yearly, per Orange Business. Misplaced totes, swiped racks, smashed bins—$10K fleets bleed $1K-$4K like clockwork. A Tier 1 auto supplier lost 35% of its $500K bin stash—$175K—yearly to supplier hoarding and zero tracking. No visibility? You’re hemorrhaging—profit’s gone before you clock it.
A logistics outfit I know tracked 1,000 bins—$50K worth—losing 25%—$12,500—yearly to theft and sloppy handoffs. Truck stops, rogue crews—bins just walked off. Without eyes, it’s a free-for-all—your budget’s toast.
2. Inefficient Asset Utilization & Hoarding
Partners hoard bins like squirrels—20% overstock here, 20% short there. A food hauler had $50K in idle totes at one hub while another stalled—$10K in delays. Drivers held bins “just in case”—production choked, orders lagged. It’s a domino effect—bottlenecks pile, trucks wait, deadlines burn.
A brewery lost 15% efficiency—$7,500—because bars stockpiled kegs—$100 each—fearing shortages. Half sat unused—$5K tied up—while brew tanks sat dry. Utilization’s your pulse—let it flatline, and you’re sunk.
3. Fleet Size Miscalculations
Guess your fleet wrong, and you’re screwed. Too few bins? $5K production halt—parts don’t move, lines stop. Too many? $20K rots in a warehouse—capital’s locked, not working. A hauler overbought 500 crates—$25K—fearing Q4; 200 sat unused—$10K wasted. Another underbought—100 short—$5K rush orders. No data, no dice—your wallet’s fried either way.
4. Lack of Tracking & Compliance
Spreadsheets are a relic—manual counts miss 15% of moves, delay returns, tank compliance. A food firm lost $30K in bins yearly—untracked supplier handoffs left no trail. Regs hit—$5K fines loomed for waste breaches. No grip? You’re begging for chaos—penalties stack, assets fade.
These aren’t hiccups—they’re profit pits. Let’s fill ‘em with fixes that hit hard.
Solutions: Optimizing the Returnable Packaging Loop
Time to flip the script—here’s how tech and smarts plug the holes, with real wins to back it up.
1. Real-Time Tracking for End-to-End Visibility
RFID, GPS, IoT—your supply chain’s hawk eyes. RFID tags ($0.20-$1) ping bins live—readers nab 5,000 in seconds. GPS tracks trucks—$1K racks don’t vanish. IoT sensors flag damage—$10K totes stay safe. That auto supplier? RFID cut losses 60%—$105K saved yearly on a $500K fleet. A hauler tagged 1,000 bins—$50K—slashing theft 40%; $20K back. It’s your radar—spot it, save it.
A brewery fitted 500 kegs—$50K—with IoT; temp spikes caught—$5K spoilage dodged—beer stayed fresh. Real-time’s your shield—chaos can’t hide.
2. AI-Powered Demand Forecasting & Fleet Optimization
AI crunches data—history, seasons, flows—to nail fleet size. A hauler cut 28% excess bins—$14K—boosting turnover 22%; $5K monthly back. A retailer shaved 300 totes—$15K—from Q4 bloat; AI pegged need at 200—$7,500 saved. You get 20% lower costs, 30% faster loops—no $10K guesswork flops. It’s your crystal ball—plan tight, win big.
A food firm forecast 1,000 bins—$50K—AI cut 200—$10K—kept flow smooth; $5K delays gone. Precision’s your profit—AI delivers.
3. Blockchain for Supply Chain Transparency
Blockchain locks every move—immutable, no disputes. A food firm slashed hoarding 30%—$15K—with smart contracts enforcing returns. Deloitte says it’s trust on lock—$5K disputes cut. A hauler tied 10 vendors—$50K bins—to blockchain; 25% faster returns—$12,500 saved. It’s your chain—bolt it, bank it.
Tech’s your toolkit—next, sustainability’s your crown.
Deep Dive: Sustainability & ESG Compliance
Sustainability’s not a sideline—it’s your 2025 must-win. Returnables are your green trump card, slicing waste, emissions, and costs while dodging regs. Here’s the full scoop.
How Returnable Packaging Aligns with Global ESG Goals
Circular economy’s the play—zero waste, max reuse. The Ellen MacArthur Foundation says returnables can slash packaging emissions 45% by 2030—50K tons of CO₂ cut yearly for big ops. The EU’s Circular Economy Action Plan demands reusable standards by 2030—$50K fines loom if you slack. US states like California and Oregon roll EPR laws—$25K hits sans compliance, per Source Intelligence. Supply chains drive 90% of emissions—returnables are your shield.
A retailer swapped 10K single-use crates—$30K—for 1K bins—$50K—cutting 20 tons waste yearly; $1K landfill fees gone. Green’s your game—play it, win it.
Case Study: FMCG Giant’s Green Slam Dunk
A top FMCG firm dumped single-use plastic—28% CO₂ drop, 50K tons waste axed yearly. RFID tracked 5K bins—$250K—AI forecast need—$200K saved, green cred soared. Regs met, fans cheered—$50K fines dodged, sales up 5%. Sustainability’s your profit play—returnables deliver.
Slashing Scope 3 Emissions
Scope 3—supply chain emissions—is 90% of your footprint. Returnables cut it—40% less raw material (no plastic churn), 20% fewer waste hauls (fuel saved), 15% tighter supplier runs (less idle). A hauler cut 10K miles—$5K fuel—with optimized loops. It’s your green armor—report clean, win big.
Financial Payoff of ESG Smarts
Green pays—40% off procurement ($50K yearly mid-size), no landfill fees ($5K saved), leaner logistics ($10K fuel cuts). Investors love it—85% eye ESG, per McKinsey—$100K grants flow easier. A firm nabbed $75K green funding—bins paid off twice. It’s your cash cow—green meets gold.
Blockchain & ESG: Future-Proofing
Blockchain’s your green badge—immutable logs prove every bin’s trip. Deloitte says it boosts ESG accuracy 30%—$20K fines dodged, investors trust you. A retailer tied 1K bins—$50K—to blockchain; 20% less greenwashing flak—$10K PR saved. It’s your edge—sustainability locks profit.
Now, let’s build your loop—step by step.
Step-by-Step Implementation Guide: How to Optimize Your Returnable Packaging Loop
No shots in the dark—here’s your playbook to a lean, green loop, with tech and grit.
Step 1: Assess Your Current Returnable Packaging Program
Audit first—map your loop, spot the cracks. Where do bins start? Where do they stall? A hauler found 30%—$60K—of bins stuck at suppliers—untracked mess. Check shrinkage—20% loss? $10K gone. Turnaround—30 days too long? $5K delays. Utilization—50% idle? $25K wasted. Ask teams—dock crews flagged hoarding; $2K fixes missed. A brewery mapped 500 kegs—$50K—found 100 AWOL—$10K lost. It’s your baseline—know it, own it.
Step 2: Implement Real-Time Tracking for Visibility & Control
Tag it—RFID ($0.20-$1) on bins, GPS on trucks, IoT for damage. Sync to LoopManager—live tracking. That auto firm cut 60% loss—$105K—tagging 5K bins. A hauler fitted 1K bins—$50K—GPS caught 20 thefts—$10K saved. Train crews—scan fast, catch alerts—$5K errors cut. A food firm IoT-tracked 500 totes—$25K—saved $5K spoilage. It’s your eyes—see it, save it.
Step 3: Optimize Fleet Size with AI-Driven Demand Forecasting
AI crunches history—Q4 spikes, slow summers—nailing need. A hauler cut 28% excess bins—$14K—boosting turnover 22%; $5K monthly back. Test it—deploy 500 bins, tweak live—$10K saved vs. guesses. A retailer cut 300 totes—$15K—AI pegged 200; $7K back. Feed data—usage, cycles—AI learns, tightens 10% yearly—$5K saved. It’s your brain—size right, win tight.
Step 4: Introduce Blockchain Verification for Supply Chain Transparency
Blockchain logs every handoff—tamper-proof, no fights. A food firm cut hoarding 30%—$15K—smart contracts pinged late returns. Set it—check-ins, damage, ownership—$5K disputes gone. A hauler tied 10 vendors—$50K bins—25% faster returns; $12K saved. Blockchain’s your chain—lock it, rock it.
Step 5: Set Strict Return Policies & Supplier Accountability Measures
Rules rule—30-day returns, $100 fines late. Alerts buzz—LoopManager nagged 10 vendors, sped 25%—$5K saved. Deposits work—$50 back fast; a firm cut delays 20%, $3K saved. Review quarterly—$2K penalties hit laggards. A brewery set 15-day keg rules—$5K delays cut—vendors snapped to it. It’s your whip—crack it, cash it.
Step 6: Measure Results & Continuously Improve
Track it—40% less loss ($20K), 30% faster loops ($15K), 25% leaner costs ($12K). Dashboards flag snags—$5K idle bins caught. Audit suppliers—$3K fines hit hoarders. Upgrade—ML cuts 10% more waste yearly; $5K saved. A hauler tracked 1K bins—$50K—shaved 15% costs; $7K yearly. It’s your tune-up—keep it roaring.
Optimize Your Returnable Packaging Strategy
LoopManager delivers—40% less loss, 30% leaner ops, 20-35% savings—$50K-$100K yearly mid-size. It’s your edge—cut waste, boost green, bank cash. Ready?
Frequently Asked Questions (FAQ) About Improving Your Returnable Packaging Loop
Got questions? Here’s the quick dirt on nailing your loop.
1. What’s the easiest way to track returnable packaging?
Slap on RFID tags—$0.20-$1 each—with a basic reader and sync to free tools like Google Sheets. It’s a quick, scalable kickoff that keeps costs low.
2. How much can returnables save me?
Big time—20-35% off packaging costs, plus 40% less shrinkage with tracking. That’s thousands yearly, backed by Grand View Research.
3. Do I need fancy tech to optimize?
Not at all—RFID or GPS gets you rolling fast. Add AI or blockchain later to level up; basics still slash waste quick.
4. How does blockchain boost my loop?
It’s your trust lock—immutable records cut disputes and hoarding by 30%, per Deloitte. No more finger-pointing.
5. Can small ops manage returnables?
Absolutely—LoopManager scales from a handful of bins to thousands. Start small, grow lean—no wallet-busting hit.